Ударный конкурс. Креативный импульс
Завершен прием проектов на "Ударный конкурс". Самое время показать вам участников, пока жюри изучает работы и выбирает победителей. Вашему вниманию представляем проекты участников из категории "Креативный импульс":
1. Барашков Дмитрий
"Мой первый самостоятельный проект с использованием 3d-принтера.
При сборке оказалось что конструкция не совсем удобная, а так же рассчитана была на обычные светодиоды, яркости которых не хватает. Пришлось использовать ws2812b и arduino pro mini. Сначала придумана и разработана 3D модель:
Потом печать на 3D-принтере (почему-то не подумал запечатлеть сам процесс). Потом сборка и программирование сия чуда:"


2. Радченко Виктор
"Макетирование – это сложный высокотехнологичный и творческий процесс. В данном посте я постараюсь рассказать, что же такого сложного в данной работе и почему к результату все относятся по-разному.😟
Итак, начнем!
Поступил один из заказов - нужно сделать макет настоящей установки в уменьшенном масштабе (конкретные цифры уже и не вспомню). Заказ интересный, начались переговоры по срокам выполнения. Пока шли все эти скучные обсуждения (не люблю данную процедуру, за что иногда подкидываю себе же дополнительной работы), решил "разобрать" всю модель по частям. Так печатать лучше: не будет поддержек, а, следовательно, и быстрее все получится отпечатать.
Заказчик был нацелен серьезно, поэтому я решил не тянуть время, а начать печатать некоторые детали. И тут всплывает основная проблема макета: не все детали, которые моделируют заказчики, можно сразу "закинуть" на 3D-принтер.
Переговоры подходили к логичному завершению (ориентировочно месяц на выполнение), а я уже готовил модели к печати. Делается это не сложно: берешь готовую модель, сохраняешь внешний контур и заполняешь максимально внутреннюю полость. Но когда их около 150 таких моделей, приходится как-то делегировать процесс. Пока я переделывал модели для печати, готовые уже создавались. Лестницы так же пришлось переделывать: при нашем масштабе они не пропечатывались. Пришлось делать их немного толще, чем в масштабе.
Масштаб подбирался таким образом, чтобы можно было создать максимальное количество деталей. Самые маленькие части и трубы печатались на фотополимере по технологии DLP (на фото зеленым цветом), остальное по технологии FDM-печати (белым цветом).
Так как общее количество деталей выходило за две сотни, то каждую модель приходилось подписывать (фото 1). Далее были распечатаны рама макета, лестница, поручни и склеены в одну модель (фото 2).
Самое интересное – это после печати собрать весь макет в одну конструкцию. Особое наслаждение видеть, как вырастает модель на глазах.
И вот модель вся собрана, покрываем грунтом и ждем, чтобы все хорошо высохло!
Начинается второй из сложных моментов – покраска. И здесь начинаются споры, кто-то считает, что сначала нужно красить, потом уже клеить, другие считают иначе. Я как раз и пошел по пути, который "иначе". Габаритные объекты покрасил аэрографом успешно, а вот с маленькими деталями возникла проблема - тяжело дотянутся до поверхности, приходилось красить кистью. Из-за этого увеличилось время покраски, так как после аэрографа краска высыхает быстрее. Но меня это не останавливало! Пару дней встретил луну на работе и все готово.
Наступил последний этап – создание акрилового купола и транспортировочного короба. Тут проблем не возникло, один день с CorelDraw и все части готовы, "кидаем" на лазерный станок и останется только собрать. Параллельно печатаем уголки для акрилового купола с углублением под гайку М3. ВСЁ, выдохнули, собираем!
Внутреннюю пленку убираем, внешнюю пусть заказчик снимает уже у себя сам). Получилось вроде бы неплохо, НО!! Почему-то уже после сборки и покраски приходят идеи, как лучше было сделать и где исправить. Причем у каждого, кто видел макет, было свое мнение: кому-то нравилось, кому-то не очень.
Мое мнение: я бы сделал чуть иначе, а также попробовал бы сначала покрасить, а потом уже клеил в одну модель. Всегда хочется доработать макет.
На этом все, друзья! Надеюсь, вы пережили со мной те эмоции, которые были у меня в момент создания макета."
3. Дарья Гевлич
"Проект "Кроксодром".
Началось все с того, что к нам обратились друзья-скалолазы. Они очень захотели подарить на день рождения подруге по скалодрому кроксы с джибитсами в виде скалолазных зацепок. Видели картинку в интернете, но нигде нельзя купить и не нашли готовых моделей для печати.
За основу взяли видео со скалодрома и модели "взрослых" зацепов. Выбрали похожие на аутентичные болты и шайбы, взяли вплавляемые втулки М3 и приступили.
Часть моделей были переделаны, часть сделана с нуля, придуман способ крепежа.
11.04.2024 подарок был вручен и вызвал бурю положительных эмоций - остальные скалолазы завидовали.
Печатали на принтере Flying Bear Ghost 5 пластиками PetG разных цветов, включая пластик Bestfilament.
Так как крепления разборные, то друзья сами построили трассы перед вручением.
Создание многоцветных картин на 3д-принтере.
Всё большую популярность в иностранных сообществах набирает HueForge – программа для создания многоцветных 3d-печатных картин.

Примеры картин. Фото с etsy.com.
Сразу стоит сказать, что нужно уметь пользоваться HueForge, сделать красиво нажатием одной кнопки у вас не получится. Не малую роль играет исходное изображение, на основании которого будет создана 3d-модель. Наиболее простой вариант – это использование картинок в стиле Поп-Арт
1. Исходные данные
Для проекта была выбрана следующая картинка:
В качестве материала будем использоваться ABS-пластик от Bestfilament, а именно цвета: черный, белый, красный, синий и оранжевый.
В качестве 3д-принтера используется BambulabP1Sс AMS (станция подачи материала), но сразу отмечу, что для HueForgeAMS не обязательна.
2. Калибровка пластика.
Я уже давно пришел к выводу, что залог успешной печать – это хорошо откалиброванная динамика и скорость потока. Запускаем тесты и выясняем, что для скорости 200 мм/с, с соплом 0,4 мм нагретым до температуры 270 градусов, оптимальный коэффициент потока для всех цветов составил 0,97, а коэффициент динамики потока – 0.015.
При калибровке красного цвета сопло сорвало несколько линий
Калибровка HueForge.
Пришло время перейти непосредственно к программе HueForge.

Я не буду вдаваться в подробности о том, как работает HueForge, на YouTube есть достаточно подробные руководства. Остановимся лишь на теме калибровки пластика.
Наша задача добавить в базу пластик ABS от Bestfilament, откалибровать его цвет и уровни прозрачности. Для этого обратимся к разделу «FilamentLibrary».
Создаем новый филамент нажатием кнопки «NewFilament» и задаем ему нужный нам цвет. Чтобы HueForgeкорректно отображал цвета в предпросмотре, нам нужно максимально точно указать код этого цвета. Один из вариантов добиться этого – сделать фотографию распечатанных калибровочных пластинок и измерить код цвета при помощи специальных программ. Для этой цели я использовал Photoshop.
В моём случае оранжевый цвет на фотографии получился темнее, чем он был на самом деле, поэтому я на глаз скорректировал его значения.
Итого, для расцветок ABS-пластика от Bestfilament получаем коды: красный - #eb1126, синий - #0776cd, оранжевый - #f45318, а черный и белый, это коды #000000, #ffffff, соответственно.
Указываем эти коды при создании новых филаментов, а также бренд пластика и его имя. Параметр «TD»оставляем пока без изменения. Его мы вычислим на следующем шаге.
«TD» расшифровывается, как Transmission Distance, но куда проще называть его уровень прозрачности. Этот параметр определяет через сколько слоёв пластик (например, белый) полностью перекроет цвет распечатанного снизу слоя (например, черного) и позволяет предположить какие градиенты будут нам доступны при печати одного, двух или нескольких слоёв.
Для калибровки этого параметра HueForge содержит специальный STL-файл, называется он «Step_Test_Square.stl» и находится в папке программу в каталоге «Tools». Перетаскиваем его в рабочее поле HueForge (параметры в разделе «General Options and Operations» должны иметь значения по умолчания), в разделе «Color Sliders» оставляем два цвета: черный до 12 слоя (1.04 мм), калибруемый цвет до 16 слоя (1.36 мм), остальные слайдеры опускаем до нуля.
Перетаскиваем тот же STL в наш слайсер, задаем толщину базового слоя 0,16 мм, толщину остальных слоев 0,08 мм, на 12 слое меняем пластик на калибруемый цвет. Печатаем.
В результате мы получаем ступенчатую пластинку, которую сравниваем с изображением, представленным в программе HueForge, и меняем значение TD в разделе «Color Sliders» для калибруемого цвета, пока картинка и пластинка не станут максимально похожими.
Для расцветок ABS-пластика от Bestfilament я получил следующие значения TD: красный –7,5, синий - 6,0, оранжевый - 7,5, белый – 2,5. Черный я не калибровал, так как он не использовался на верхних слоях.
3. Получение 3д-модели и инструкции по смене пластика.
После калибровки пластика начинается творческий процесс. Цвета из раздела «Filament Library» мы перетаскиваем на слайдеры в разделе «Color Sliders», регулируем их высоту, подстраиваем 3d-модель в разделе «Model Geometry». После всех манипуляций и сохранений проекта, в его папке появляется STL-файл и инструкция для печати.
4. Печать
Запускаем слайсер, добавляем 3d-модель и согласно инструкции задаем параметры для печати (заполнение и высоту слоев). После чего указываем слои, на которых будет осуществлена замена пластика. Главное преимущество HueForge в том, что для создания цветных картин не обязательна станция подачи материала (как AMSу Bambu Lab). Смена цвета происходит только в начале слоя, что позволяет осуществлять это и в ручном режиме. Для печати картины Дарта Вейдера пятью разными цветами, замена филамента нужна всего лишь 4 раза на 5, 11, 17 и 20 слое. Общее время печати заняло около 8 часов и вот результат:
Итоги:
HueForge достаточно перспективная программа, которая позволяет создавать действительно впечатляющие картины, которые выглядят необычно и свежо. Многие иностранные производители пластика уже создали для неё библиотеки своих материалов, надеюсь, когда-нибудь мы увидим официальную библиотеку и от Bestfilament."
5. Трунин Евгений
Мое увлечение 3D-печатью берет начало с 2015 года. Но недавние достижения сообщества, в частности прошивка Klipper, вселили надежду на то, что мои старички еще поработают. Закупив Nebula Pad, я разогнал своего нового Ender 3v3 SE и принялся изучать возможности усовершенствования технологии печати.
Для меня 3D-принтер – это станок для финального производства изделий. Идеологически я отвергаю какую-либо постобработку напечатанных моделей: шлифовку, химическую обтравку и прочее. Моя цель – печатать сразу качественные изделия, лишенные характерных "болячек" бюджетных 3D-принтеров. Однако даже куб мне не удавалось напечатать достаточно идеально по меркам внутреннего голоса перфекциониста, не говоря уже о художественном изделии.
Поэтому я решил изучить, какие решения может предложить сообщество для этой нетривиальной задачи. И ответ был найден достаточно быстро – fuzzy skin.
Эта функция позволяет менять геометрию печатаемого объекта, добавляя шумы на его поверхность и перенося швы в случайные места. Благодаря этому удается избавиться от видимых швов, а отпечатанная модель выглядит более качественной, лишенной воблинга и смещения слоев, словно так и задумано. Однако при этом возникает проблема с печатью сложных или составных художественных моделей с сочленениями или резьбовыми соединениями. К счастью, будучи гуру Blender, я могу задать нужный шум там, где это необходимо.
Первой моделью для испытания технологии fuzzy skin я решил выбрать складной меч.
Эта функциональная и интересная для печати модель показалась мне наиболее подходящей для теста. Необходимо было напечатать ее сначала в классическом режиме, а затем с применением шумов на стенках для скрытия дефектов печати. Однако модель не поддавалась печати одним объектом, когда клинок печатается в закрытом виде вместе с рукоятью. Поэтому пришлось печатать в несколько этапов, останавливая процесс для загрузки клинка в рукоять прямо во время печати. К тому моменту, потратив несколько дней на печать и осмысление метода, у меня возникла идея: "А почему бы не придать художественный смысл шуму на стенках?" Так я принялся моделировать свою версию этого меча, но уже в японском стиле. Рукоять я смоделировал очень детально, с мельчайшими подробностями хлопковой обмотки катаны. Лезвие оставил от исходной модели, и полетела печать. Печатал, конечно же, пластиком от Bestfilament, ведь качественный материал - еще один ключ к хорошему результату, что тоже требовалось учесть. И результат меня порадовал.
Рукоятка действительно напечаталась крайне качественно, не без косяков, но этот блин комом точно не назовешь) в руке эта она ощущается очень интересно и невозможно понять из какого материала сделана, что мне показалось совершенно неочевидным исходом эксперимента и я решил повторить и усилить этот эффект.
Однако сам клинок оставлял желать лучшего. Он был довольно хрупким, а заметный шов на боку не позволял раскладывать его на всю длину.
Далее последовали эксперименты с режимами печати и изучение нового для меня слайсера Orca Slicer (на мой взгляд, лучшего на данный момент для нарезки моделей). После многочисленных попыток перенастроить принтеры, пробных печатей и тестов по переносу швов под разными углами, я окончательно пришел к выводу - шва на клинке быть не должно! Но как этого добиться? Правильно, напечатать модель в режиме вазы! Поскольку лезвие я вкладываю отдельно, такой метод вполне приемлем, к тому же помимо очевидного избавления от шва он добавляет прочности отпечатку - что не может не радовать.
Как вы понимаете, прошло еще некоторое время, в течение которого я, словно ребенок, размахивал свеженапечатанной, но уже потрепанной игрой катаной. Теперь у меня были технологии бесшовной печати клинка и красивых отпечатков для рукояти. Но я не торопился и решил улучшить ее еще больше. Классическая катана имеет изогнутое лезвие, заточенное только с одной стороны. Для этого пришлось слегка увеличить габариты самой модели и согнуть ее под углом лезвия, что никак не сказалось на художественных характеристиках. Также я учел ошибку с углом печати обмотки клинка и теперь витки идут двойным слоем, не позволяя нити отвисать, как соплям. Для гладкой формы основы рукояти я сделал текстуру отбитого металла, что должно было скрыть воблинг и придать отдельный шик изделию. Торец я оставил гладким, о чем позже пожалею. На этот раз для печати я использовал пластик Creality Matte Black. Он не только придает распечаткам красивый матовый цвет, но и тактильно ощущается как софт-тач пластик, что должно было улучшить и тактильные характеристики модели. Пришло время печати!
Лезвие я печатал по частям и вкладывал в рукоять уже во время печати. На мой скромный взгляд, модель напечаталась отлично! Выглядит стильно, идеально складывается и раскладывается, швов на лезвии нет, а на ощупь совсем не кажется пластиковой! Показывал ее друзьям, в том числе никак не связанным с 3D-печатью, и все спрашивали, из какого материала она сделана. Но теперь-то мы знаем, что дело не только в пластике!
6. Герман Андрей
Мой проект - детский конструктор. Я в детстве очень любил играть в различные конструкторы, поэтому один из них попытался воспроизвести.
Китайская компания Tukzar сейчас производит аналогичный, практически копию того конструктора, которым я играл в советское время. Он называется Multiform TZ-8269.
Его элементы все одной формы, изготовлены из гибкого пластика разных цветов. Он мне нравится тем, что при малом весе элементов можно строить большие объёмные конструкции.
Но у меня в наличии был только пластик PLA И TPU, один твердый, а другой слишком гибкий. Поэтому я использовал PLA, но с креативным подходом.
Для придания гибкости я использовал шарниры, а для соединения элементов между собой придумал защёлки.
Затем я создал 3d-модели двух элементов - одного с продольным изгибом, а другого с поперечным и распечатал на принтере Creality 3D PRO, размножив в необходимом количестве.
В итоге получился конструктор с достаточной жесткостью, чтобы создавать фигуры довольно больших размеров без потери их формы.
Вы можете оценить результаты моей работы по прилагаемому видео.

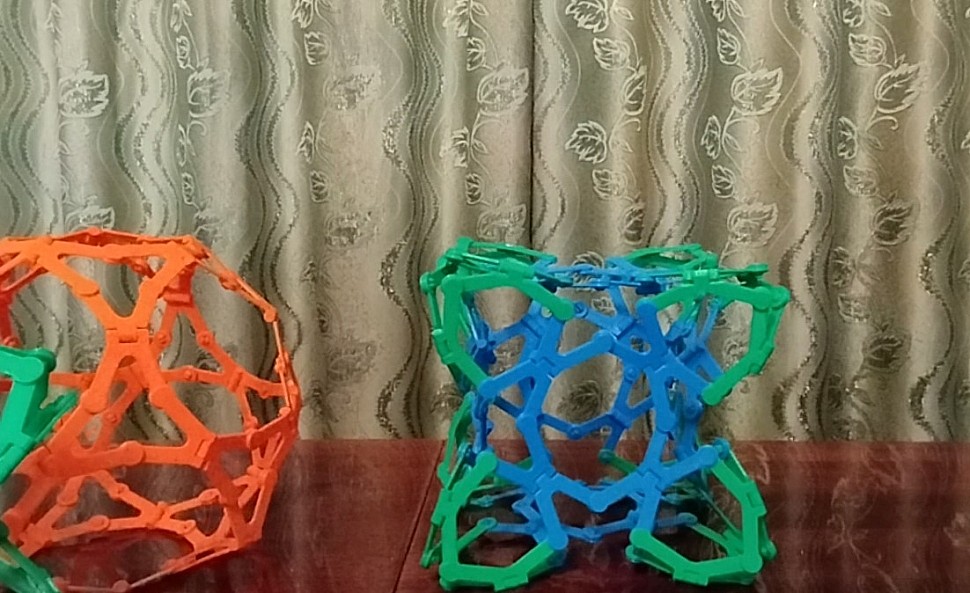
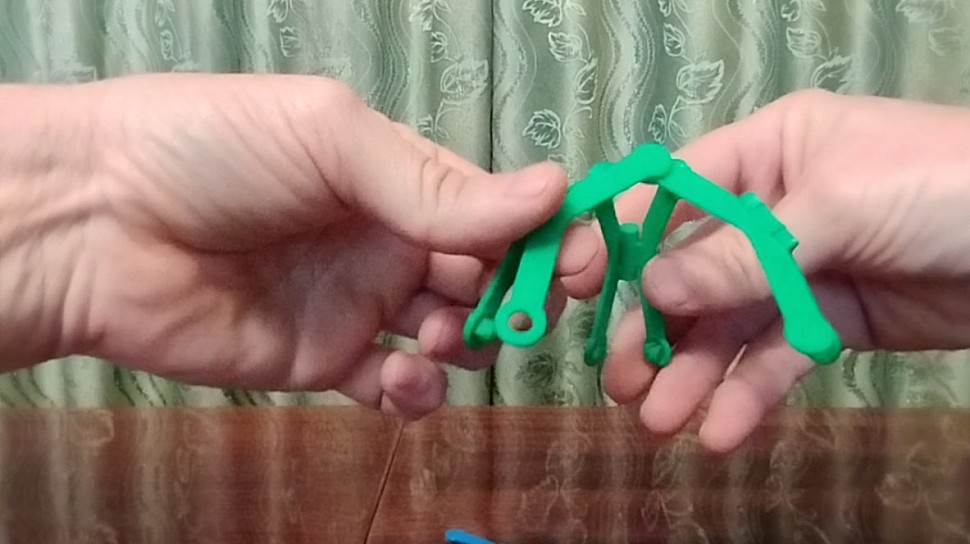
7. Кискин Евгений
Дед воевал в Сталинграде от и до, хотел его табельный смоделить.
Напечатать сложновато))) в 3ds Max и Substance.

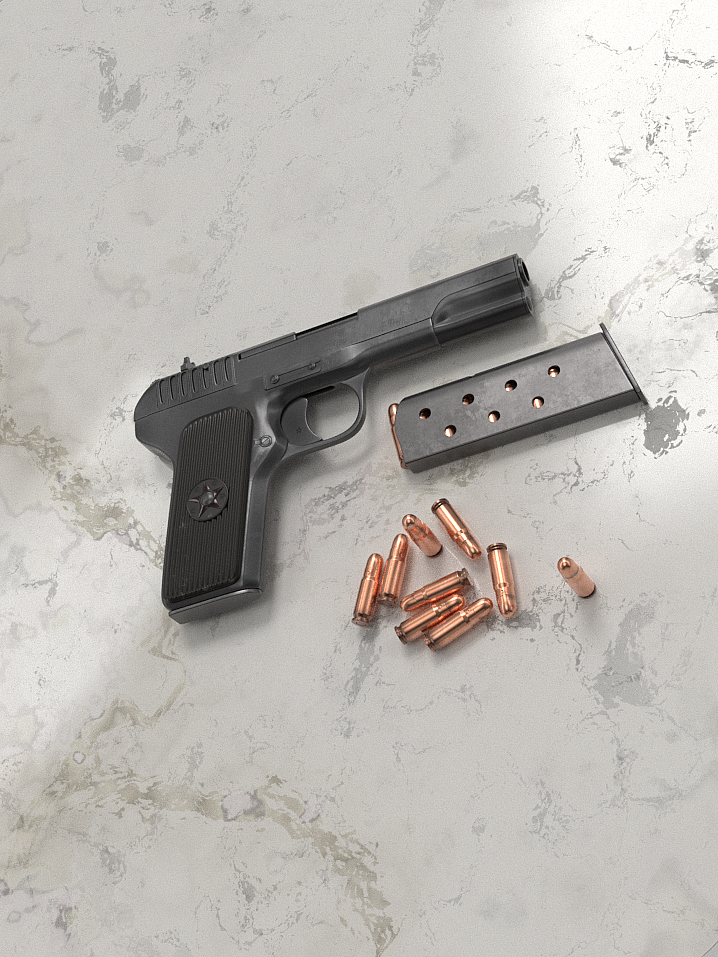
0 комментариев